Objectives:
-
To
develop contact transducer models (flaw and noise predictions) for
use in probe design and technique development/evaluation, including
tolerance variation assessment
-
To
work with industry partners to validate, model and develop usable
software tools in typical engineering environments
Approach:
- Define typical
applications
- Develop tool that
considers component geometry, (non-parallel surfaces, surface curvature,
defect orientation, defect location, flaw morphology), surface roughness,
and material effects (noise, attenuation)
- Develop a tool
for probe design, technique evaluation, and tolerance variation that
addresses wedge coupling, beam shape, multiple sound paths, multiple
UT modes (i.e. corner trap, longitudinal reflection, shear, tip diffraction,
and surface wave)
|
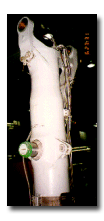 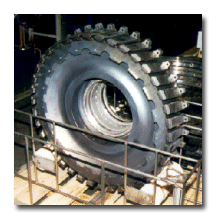
Service induced
cracking is often an issue in complex geometrical features such as lugs,
attachement points, and other complex components.
|